Missed parts 1 and 2 in this series? Never fear, you can check those out via the links below to see the progression of the Spiritus plate carrier design from a non-functional pattern prototype through to the field-ready example featured in this post .
This much later example (but still within the prototype phase) gets very close to the eventual commercial release of the LV-119 in terms of feature set, though it goes about some things in slightly different ways. A crucial difference to highlight between this MT and the retail LV is that this example is made entirely from the same laminate fabric that I discussed in part 2, whereas the current production 119 carrier uses almost no laminated fabric at all. That is set to change drastically, with the all-laminate LV-120 due to release imminently at the time of writing, however for now the
It is worth mentioning at this point that the first examples of Spiritus PCs I saw were at the 2018 SHOT Show, where the No-Vis, Low-Vis and Hi-Vis/Tactical were displayed. This example fits in with the feature set of the Low-Vis in that it can mount a placard at the front but cannot accept a zip-on panel at the rear, however the overall name of the product family was the Mixed Tactics PC, hence I have used that name throughout all of these articles. It is very much worth referencing my earlier post from the Spiritus booth at that show via this link, if you are interested in these particular items of gear.
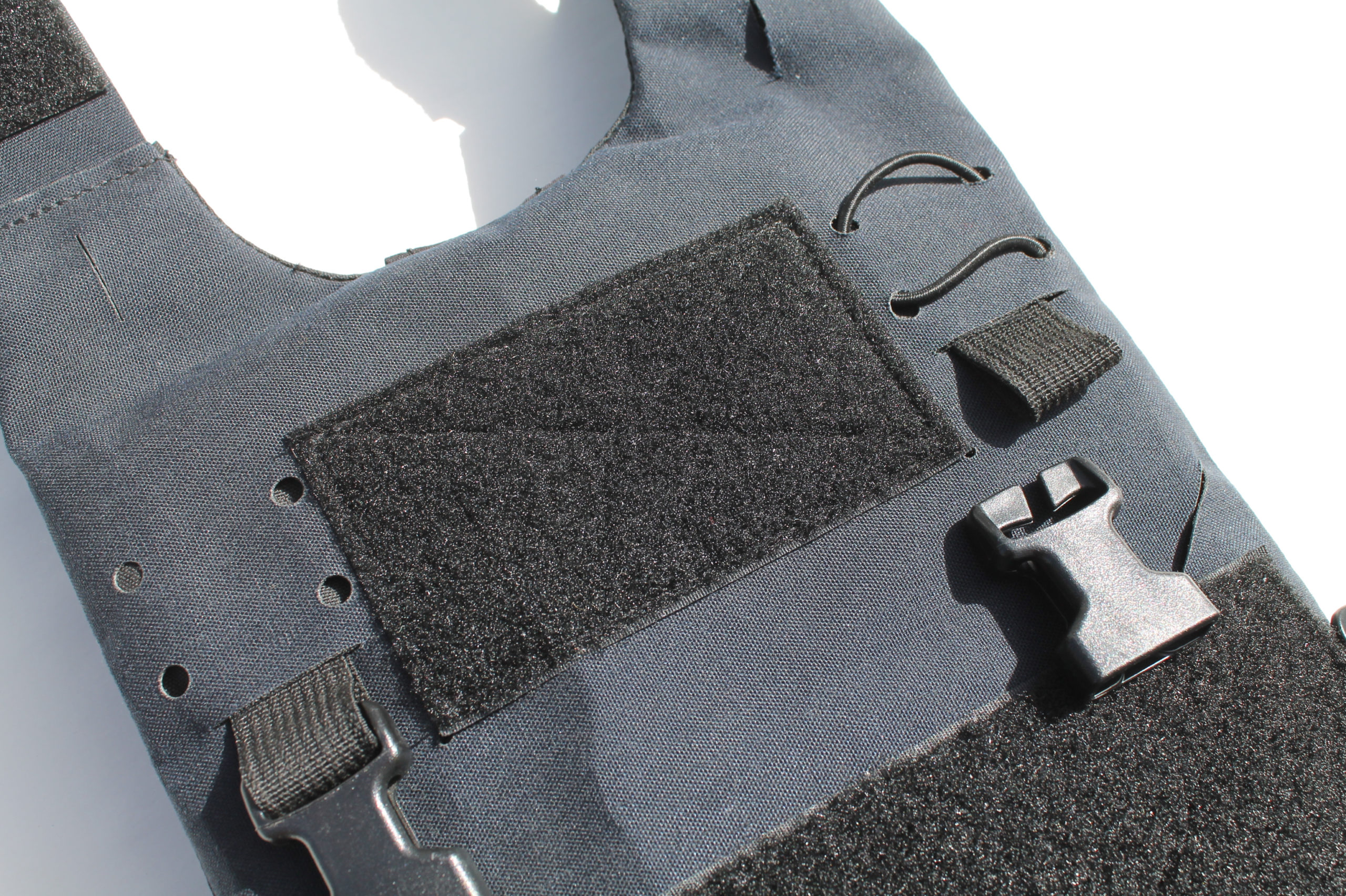
As mentioned, in terms of features and actual functions that the plate carrier can provide its’ wearer, this example is very close to the LV-119 but achieves those features and functions in slightly different ways due the material differences. Mounting for the placard is essentially unchanged between prototype and production design of course since that system utilises 1″ webbing/buckles and a loop field, but the cable management on the chest area is quite different, given the use of laminate on this prototype vs the standard nylon and webbing used on the 119.
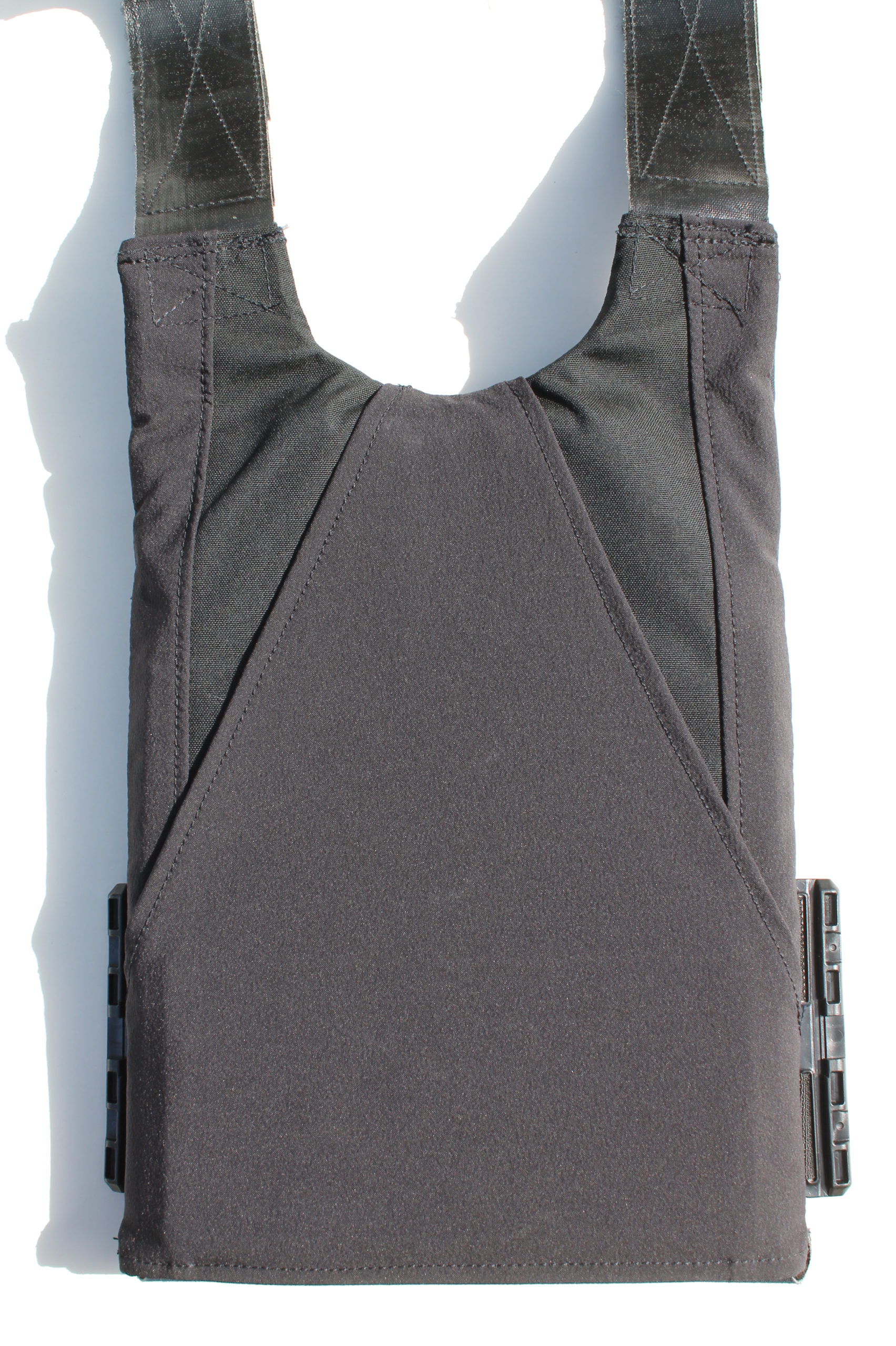
Inside of the front plate bag the layout on this prototype is almost entirely representative of the final article, with stretch panels on the sides to accommodate different plate thicknesses and a document stash pocket also made from the stretch fabric. The stitching on the diagonal lines was slightly beefed up for production, but that is just about the only change.
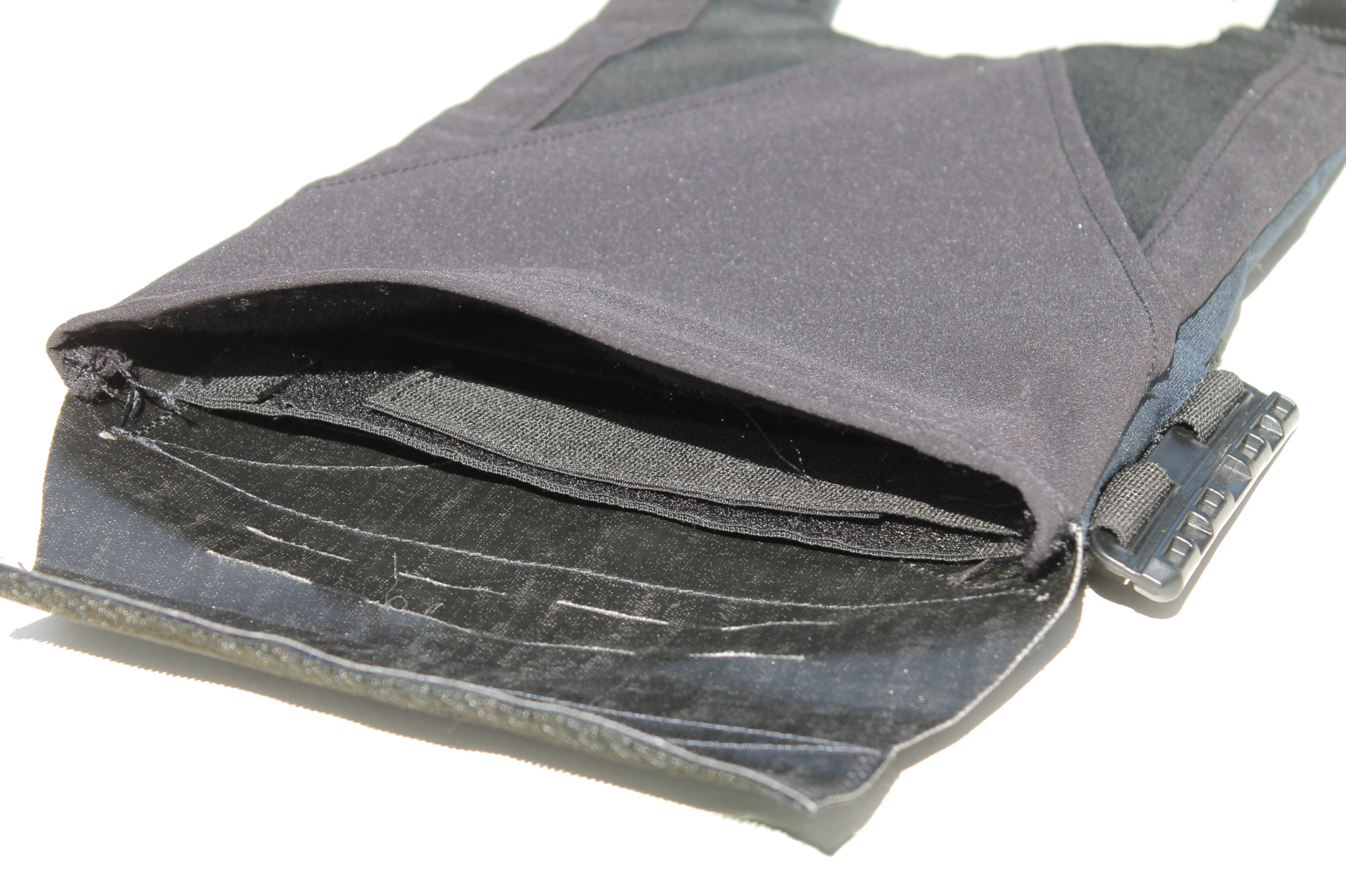
On the inside of the front plate bag flap you can see above, the black synthetic fabric that forms the rear/inner face layer of the laminate material is clearly visible. I cannot state for a fact what that inner face fabric happens to be, but it is very densely woven, slick to the touch and highly reflective; possibly a type of polyurethane.
This would make a poor choice for the outer layer of a tactical product given the high shine and I would imagine it only comes in black, but to my knowledge it is has a much higher tear and tensile strength than 500D Cordura, so it makes complete sense as a reinforcing inner layer.
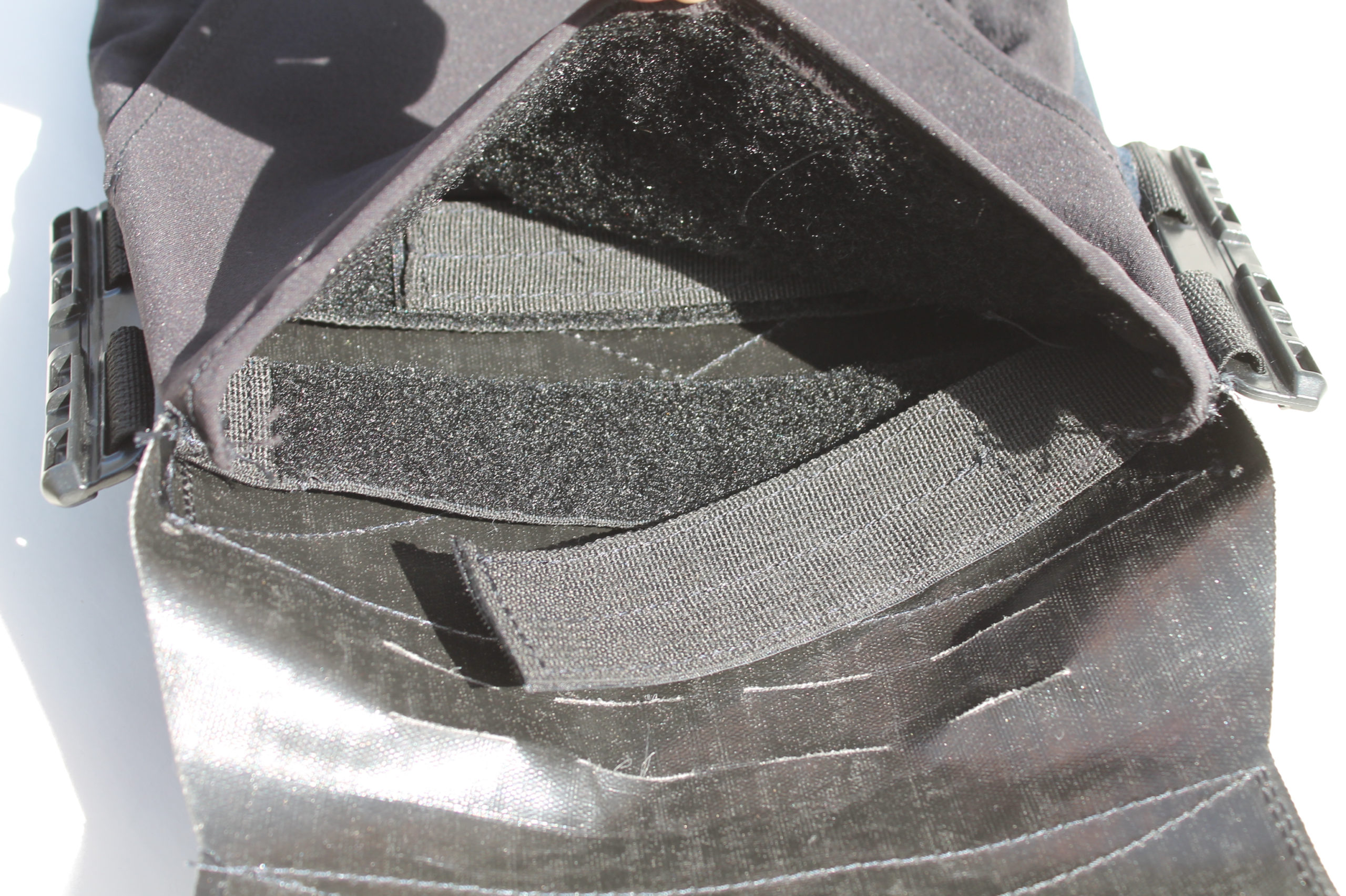
An interesting aspect of this prototype that was (sensibly) omitted on the production carrier is the ability to completely remove the 1.5″ loops that facilitate attachment of FirstSpear Tubes to the front plate bag; in this case the longer 4″ model Tuebs. For demonstration above I have disconnected the velcro on the lower loop assembly, while the upper is fully locked in to place as it would be for use. These two pairs of 1.5″ webbing straps facilitate both the option to completely remove the Tubes and also to adjust them to a fairly significant extent (which permits additional cummerbund sizing alterations).
While this feature is very nice to have, especially if you don’t use a Tubes cummerbund, the thickness of the webbing and velcro takes up a comparatively large amount of space inside the plate bag. I think it may have been necessary during the prototype phase as the field repair/split bar Tubes possibly were not yet in production at the time. The 119 production solution of simply stitch 1.5″ loops on to the outer edges of the front plate bag exterior and supplying split bar Tube hardware alleviates the issue of taking up valuable plate space, plus shaves a few oz/g in weight and also cuts a few dollars from the cost; once you factor in extra cut and sew time.
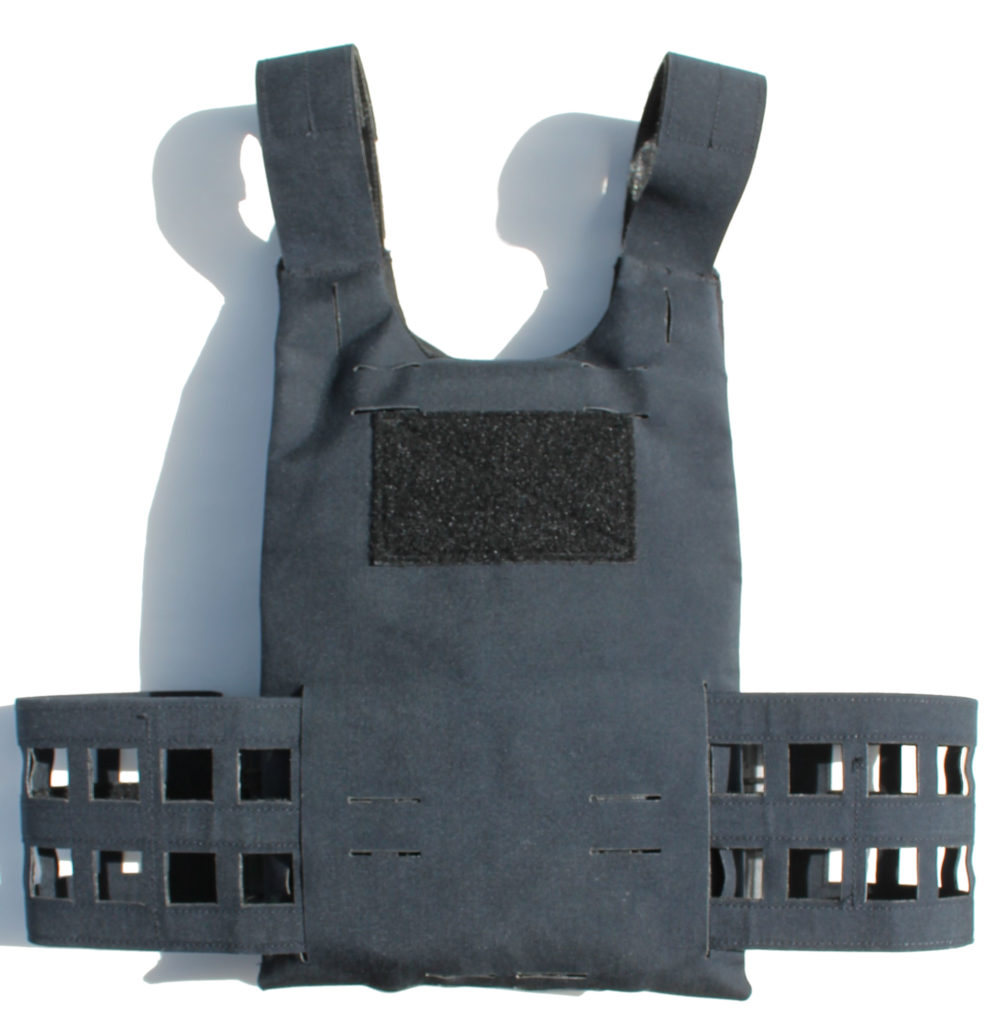
On the rear, there is no pair of zips for attachment of a back panel on this particular model, just a loop field and slots both both cable management and attachment of an optional drag handle. I have not pictured the lower internal area where the cummerbund attaches, but there is a grid of circular holes which is essentially just the same as that found on the production LV-119 rear bag.
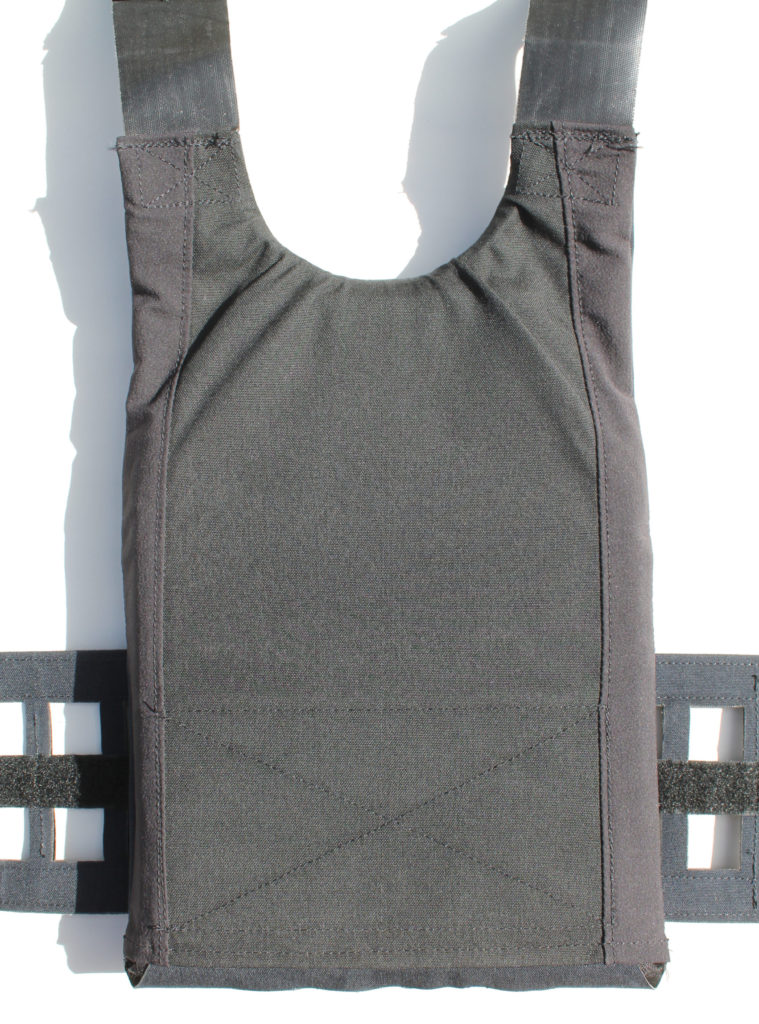
The inner face of the rear plate bag is mostly plain, with the the same stretch panels at the sides as on the front bag, allowing for a tight and slop-free fit around ballistic plates of a wide range of thicknesses. Most modern carriers incorporate such a feature in some form or another using stretch panels or adjustment tabs, though it was not quite as common during the design and testing phase of the Spiritus PC line.
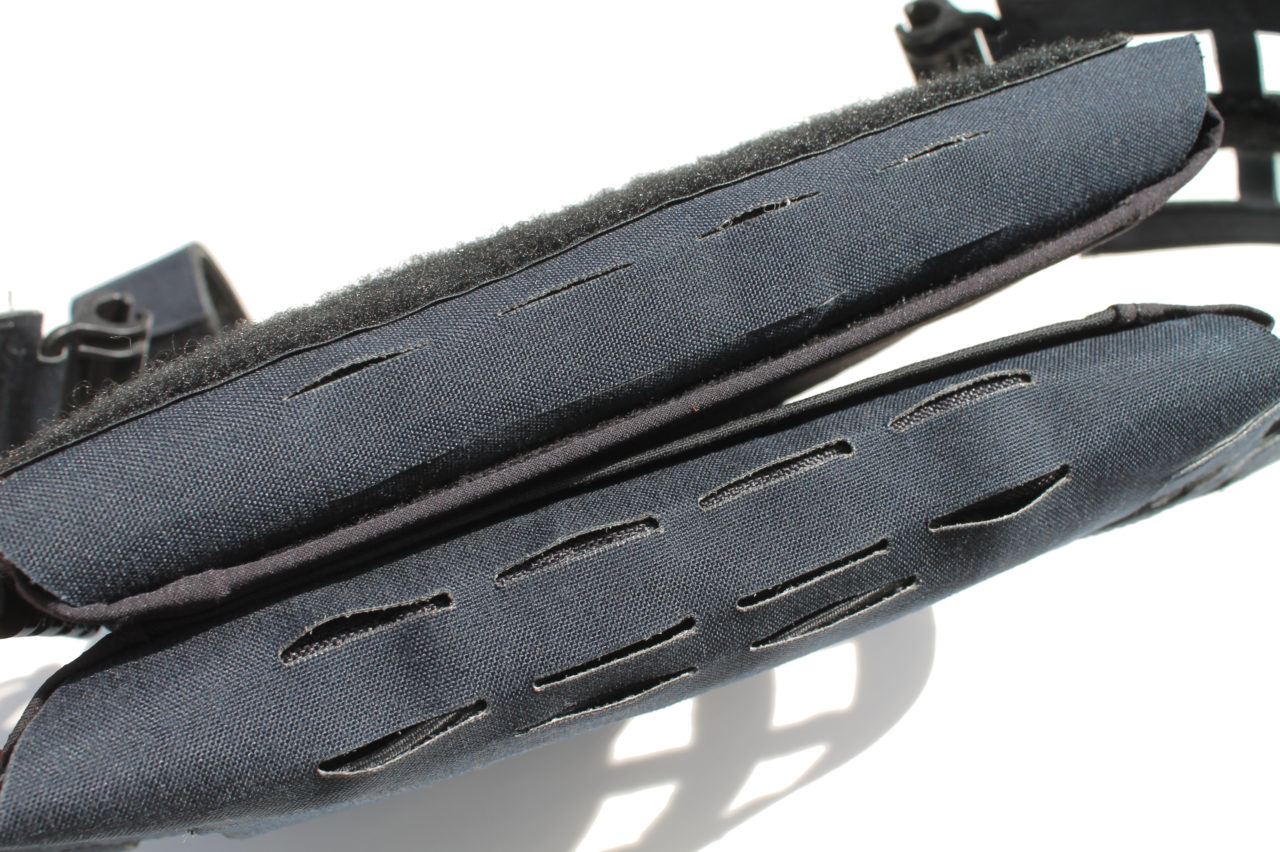
As with the previous iteration (part 2, in MC), there are PALS style slots cut in to the flaps that secure the plates in the base of each plate bag. These could be part of the cable management functionality built in to the carrier, or potentially a way to integrate other nylon products like dangler pouches, likely a combination of both.
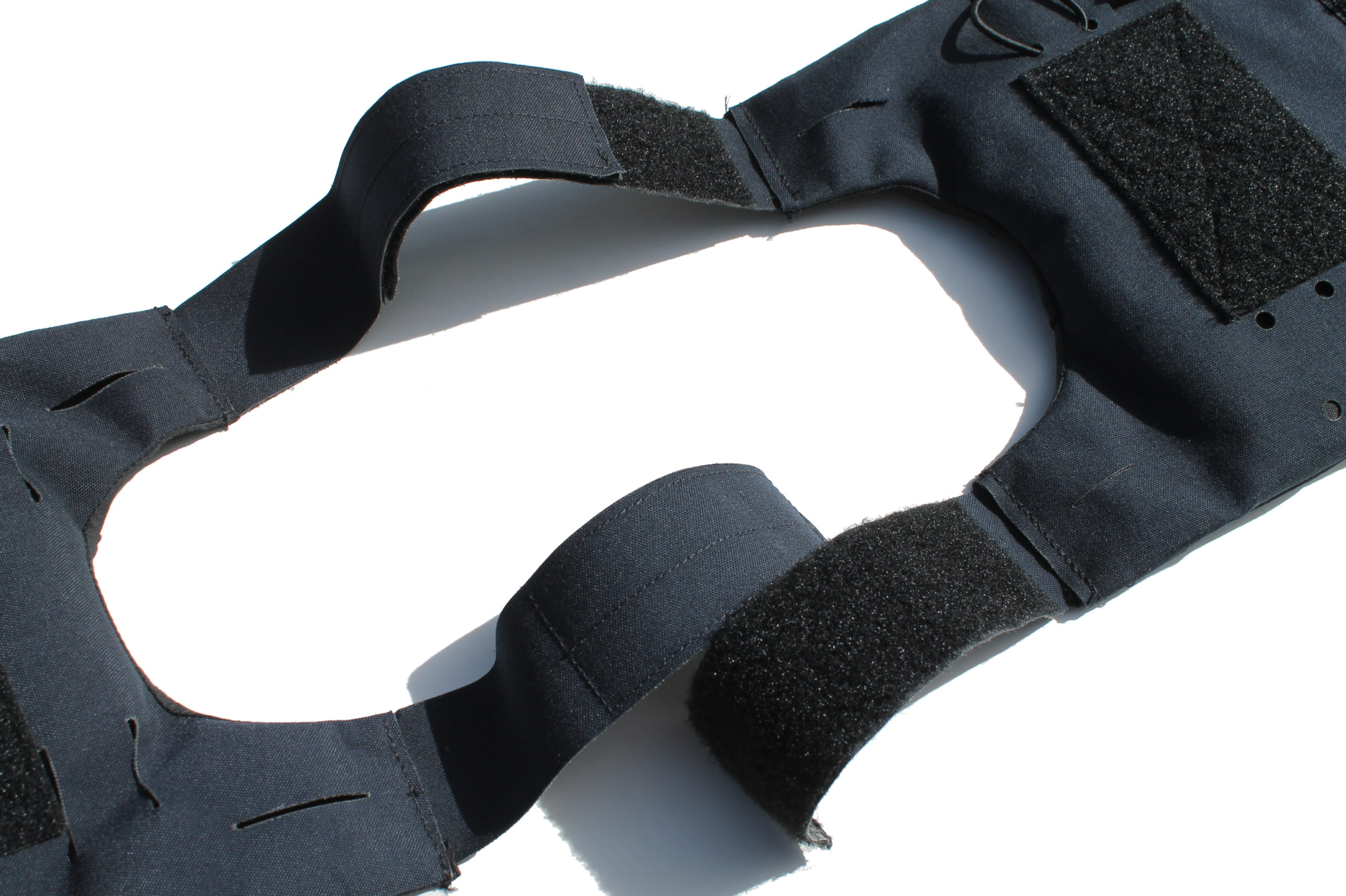
On this particular example, the shoulder strap arrangement works in the same way as the commercially sold carrier, however the base fabric is the cordura laminate. On the 119 the hook and loop materials are stitched on to a Trelleborg Hypalon or HANK type material.
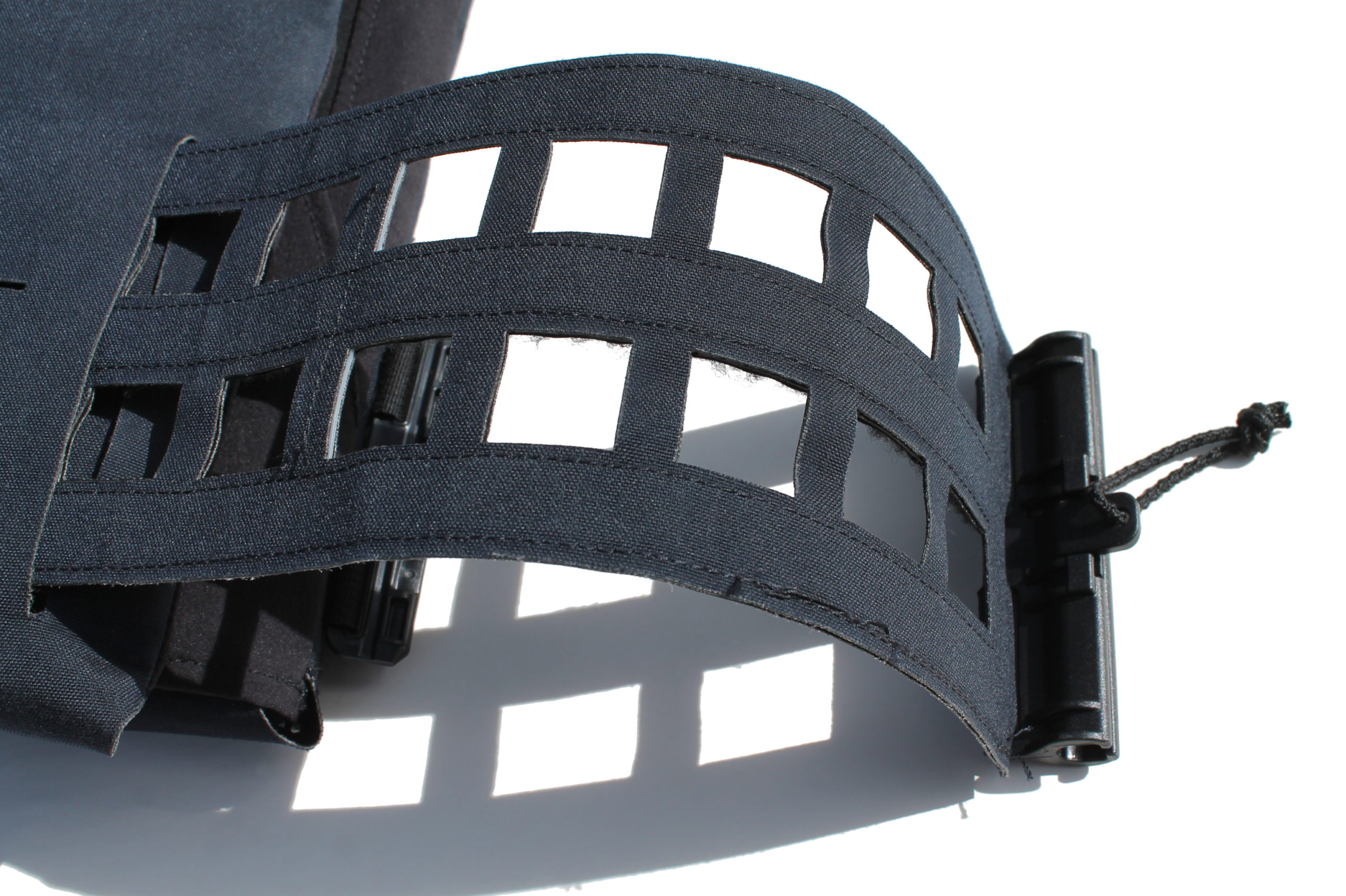
Last but very much not least, the cummerbund is a very interesting aspect of this specific prototype carrier. Presumably the concept with the entire design of this PC system was to use laser cutting of laminate nylon as much as possible in order to automate more of the production process. Bearing in mind, that up to the mid-2010s the tactical soft goods industry was predominantly building out of single layer 500D with sewn 1″ webbing to create PALS grids. For most companies the move to laser cutting and negative space PALS was only just beginning, and some had not even started that transition yet.
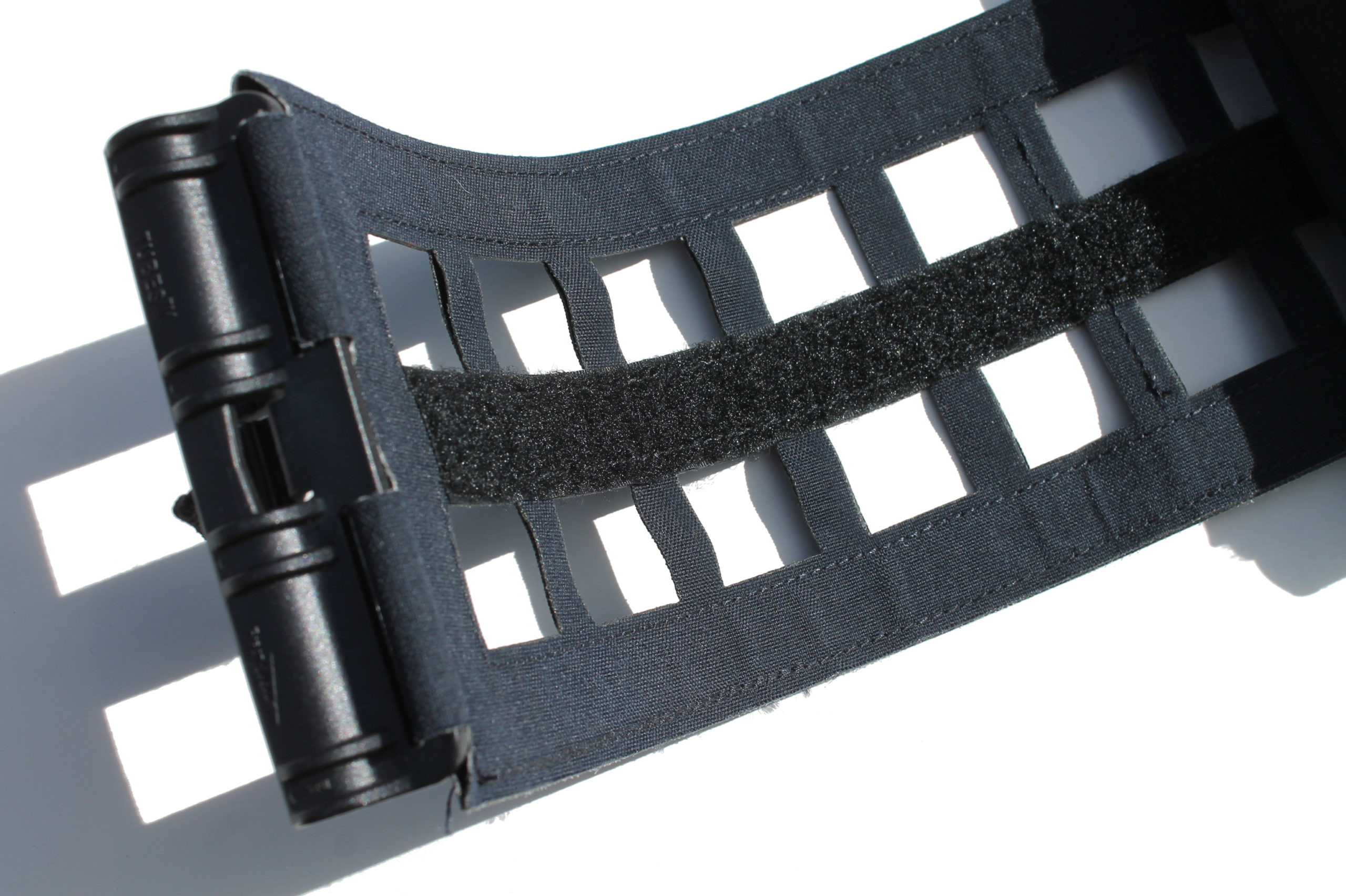
While it does appear quite different, the basic principle of this cummerbund is the same as the ‘MOLLE Tubes Cummerbund’ that was released with the LV-119 and is still sold at the time of writing. The main difference lies in this prototype being laser cut from a rectangle of laminated cordura fabric, whereas the commercial release uses strips of standard 1″ webbing, which has generally been much more commonly used in skeletal cummerbund designs across the industry. Since the basic structure of this cummerbund does just consist of 3 long horizontal strips that are an inch wide, the material change is entirely understandable when you bear in mind the issues that Spiritus had with this laminate fabric (and potentially others that were tested but aren’t publicly known).
If you have read all three of my entries here on the site covering the different Spiritus Plate Carrier prototypes, then firstly thank you for your viewership and I hope the content was interesting and informative. Again, hopefully, you will have gotten a good overview of one potential pipeline for the way a new piece of tactical gear can be developed and some of the different phases. Most importantly a big thanks to my mate (who I shall keep anonymous) from across the pond who donated these prototypes in order that they could be featured here, it is much appreciated!
1 Pingback